Spur gear slewing drive is a rotary drive. Due to the different types of drive teeth, it can be divided into straight-tooth rotary drive and helical-tooth drive, both of which are full-circle rotary drive reduction transmission mechanisms that inherit the driving power source. The previous article has already introduced the difference between the spur gear drive and the slew drive. I will not introduce it in detail here. Today, the Lunda bearing manufacturer will give a brief introduction on the installation methods of the spur gear drive. I hope it will be helpful to everyone.
Installation method of spur gear drive
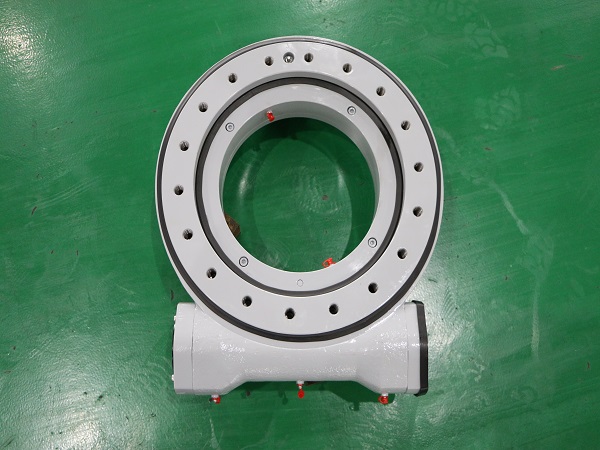
1. Fixed installation with solid shaft
This installation method is to connect the output shaft driven by the spur gear with the metallurgical machinery through couplings, sprockets, gears, pulleys, etc., and the spur gear drives the bottom anchor bolts to firmly install the spur gear drive on the structure On a solid, vibration-free foundation. At present, most spur gear drives can adopt this installation method.
For large spur gear drives, threaded holes should be machined on the body feet to adjust the installation position with adjusting bolts; for the spur gear drive of the luffing mechanism, pins should also be used for locking to prevent movement during installation .
2. Single-point floating installation of hollow shaft
This installation method uses the output shaft driven by the spur gear as a hollow shaft and is connected to the transmission shaft of the working machine through an expansion sleeve. The entire driving device, including the motor, coupling, brake, and reducer, is installed on the support of the transmission device. Seat, and then supported by a ball hinge or bearing.
The installation principle is that the bearing point of the spherical hinge deviates from the center of gravity of the transmission device by a certain distance. In the working state, the bending moment caused by the eccentricity of the support point can be balanced with the bending moment caused by the load of the driving device. Therefore, the transmission shaft is not affected by the theory. Additional force.
3. Hollow shaft suspension installation
In this installation method, the output shaft driven by the spur gear and the metallurgical machinery shaft are connected by an expansion sleeve, and the support is completed by the output shaft and another torsion rod. This installation method is relatively simple, saves floor space, and can reduce the weight of the whole machine, and is suitable for transmission devices that transmit power from a vertical direction.
Spur gear drive installation is a delicate and complex task with high technical requirements. The operating procedures and design data must be strictly observed during operation. The general installation sequence is: equipment leveling and alignment, cleaning and assembly, adjustment and trial operation.
After understanding the installation methods of spur gear drives, the spur gear drive manufacturers will introduce some precautions in the installation of spur gear drives. I hope it will be helpful to everyone.
Precautions for installation of spur gear drive
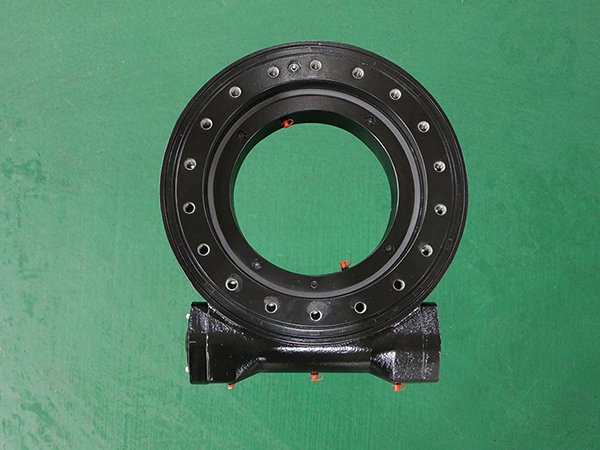
1. Cleaning and inspection: clean the spur gear drive installation shaft before installation and use, and check whether the installation shaft is bruised or dirty. When the spur gear drive is installed in an inclined manner, ensure that the high position of the gear shaft bearing is lubricated by the gear oil in the box, and ensure that the gas in the box can be discharged from the high position of the box.
2. Keep the mating interface flat: When assembling the spur gear drive with the actuator and the prime mover, the connecting flange should be cleaned and polished to ensure the flatness of the connecting part of the connecting flange, to ensure that it is flush, and all bolts on the flange circumference should be matched. , Fastening.
3. Keep balance: The assembled transmission components (couplings, sprocket) should be kept in rotation balance, so as not to cause impermissible radial force or axial force. The internal thread of the assembly fixture and the shaft end is usually used, and the transmission part is pressed in with a bolt, otherwise it may cause damage to the internal parts of the spur gear drive.
4. Do a good job of leveling: The spur gear drive installation must be rigidly fixed on a solid horizontal foundation or a vertical frame, and the leveling must be done. It is necessary to ensure that the coaxiality of the prime mover, coupling, spur gear drive, and actuator is consistent, so as to avoid additional stress on the input and output shafts and bearings of the equipment and cause damage to the equipment input and output shafts and bearings.
5. Control the shaft gap: the coaxiality of the two connected shaft extensions should be controlled within the range of φ0.1mm, and there should be a gap of 2-8mm between the end faces of the two shaft extensions. The value of the gap depends on the specific equipment connected to the spur gear drive. Depending on the situation, it is necessary to ensure sufficient load transfer capacity and to ensure that the bearings driven by the spur gear are not subject to additional axial force.
6. Add gear oil: The grade of oil should be the spur gear drive value, or the oil equivalent to the oil should be used. And the amount of oil must be correct, and each spur gear drive has a sign with the grade and quantity of oil attached. The oil mirror is a display mirror of the oil level driven by the spur gear. On the side of the spur gear drive, the oil level should reach the upper and lower positions of the middle of the oil mirror when filling oil.
Spur gear drive lubrication and oil injection method
The lubrication effect has a great influence on the spur gear drive. If the lubrication conditions are not good, the heat generated by the spur gear drive will increase and its carrying capacity will decrease. Therefore, the lubricating oil and the amount of oil must be selected correctly to effectively ensure the normal operation of the spur gear drive transmission and prolong its service life.
Under normal circumstances, the lubrication method adopts oil pool lubrication and natural cooling; and for high-power spur gear drive or insufficient thermal power, pressure circulating oil lubrication or additional cooling devices can be used for cooling.
Under normal operating conditions, when the ambient temperature is (0~35)℃, or using circulating oil lubrication, choose medium-duty industrial gear oil 220#; when the ambient temperature is (35~50)℃, it is recommended to select medium-load Industrial gear oil 320#. In addition, the spur gear drive should be replaced with lubricating oil after the first 400 hours of operation.
What are the installation methods of spur gear drive? I believe you already know it. During installation, you can choose a suitable installation method according to the specific conditions of the machine to which the spur gear drive is adapted. Of course, some precautions during the installation process have been introduced by the spur gear drive manufacturer. Up. In addition, if you have any questions about the installation or use of other spur gear drives, you can call us Longda Bearings, and welcome your calls.