What to Consider When Sourcing a Cross Roller Slewing Bearing: A Precision Buyer’s Guide
What Is a Cross Roller Slewing Bearing?
A Cross Roller Slewing Bearing is a type of slewing ring that uses cylindrical rollers arranged in alternating 90-degree directions (crossed), allowing it to simultaneously support radial, axial, and moment loads with high precision and rigidity. It is specifically designed for applications where high positioning accuracy, smooth rotation, and minimal backlash are essential.
Unlike traditional ball bearings or three-row designs used in heavy equipment, cross roller slewing bearings shine in precision engineering sectors such as robotics, medical devices, radar systems, and semiconductor production.
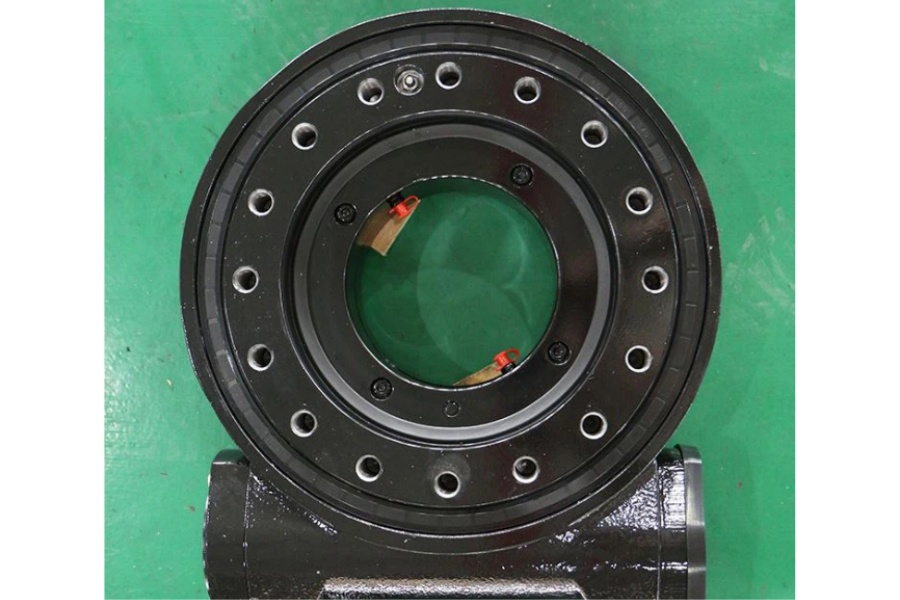
Structure and Key Features of Cross Roller Slewing Bearings
Core Design Elements:
Rollers arranged orthogonally to maximize load contact area
Single raceway groove, usually hardened and precision ground
High stiffness and low friction
Compact size compared to other bearing types with similar capacity
Internal or external gear options depending on the drive system
Benefits of Using Cross Roller Slewing Bearings
Superior Rotational Accuracy
Ideal for applications where angular deviation or backlash is unacceptable.
Minimal Elastic Deformation
Thanks to the cross arrangement of rollers, it handles moment loads exceptionally well.
High Load Capacity in All Directions
One compact unit handles axial, radial, and overturning loads—reducing system complexity.
Compact and Lightweight
Perfect for machines where space and weight are critical factors.
When Should You Choose a Cross Roller Slewing Bearing?
Use cross roller slewing bearings when:
High angular positioning accuracy is required
You’re building servo-controlled turntables or robotic bases
The application involves repetitive motion with minimal wear tolerance
The device operates under light to moderate load but with strict precision demands
LDB Cross Roller Slewing Bearing Solutions
LDB, a leading manufacturer and supplier, offers precision-engineered cross roller slewing bearings with the following specifications:
LDB-CR Series – Cross Roller Slewing Bearing
Outer Diameter: 200mm to 1600mm
Gear Type: Internal, external, or non-geared
Precision Class: P5 and above available upon request
Application Areas: Industrial robots, indexing tables, medical scanners, machine tools
LDB bearings are made from 50Mn or 42CrMo and undergo deep quenching for surface hardness and long-term wear resistance.
Key Considerations When Sourcing
Precision Grade and Backlash
Choose P5 or better tolerance levels for high-precision platforms
Minimize backlash through fine grinding and preloading if necessary
Raceway Hardness and Finish
LDB ensures 55–62 HRC hardness with ≤Ra0.8 surface finish on raceways
Lubrication and Sealing
For cleanroom or medical applications, use food-grade or low-volatility lubricants
Optional dust-proof seals for electronics and optics industries
Mounting Style
Most LDB models support both face-mounting and base-mounting configurations
Custom Gear Profile
LDB can customize the gear module, pressure angle, and tooth profile for integration with stepper/servo motors
Application Scenarios
Industry | Typical Application | LDB Solution |
Robotics | Base joints, rotary axis | LDB-CR Series |
Medical Equipment | CT/MRI scanner rotation | Low-noise, sealed model |
Semiconductor | Wafer handling robots | Anti-static variant |
Aerospace | Antenna pointing systems | Lightweight precision |
Machine Tools | Indexing tables, measuring platforms | Preloaded low-runout unit |
Price Reference for Cross Roller Slewing Bearings
The price of a cross roller slewing bearing varies based on size, precision class, gear type, and material:
Outer Diameter Range | Price Range (USD) | Gear Type |
200mm–600mm | $200 – $800 | Gearless/Int |
600mm–1200mm | $800 – $1600 | External Gear |
1200mm+ | $1600 – $3000+ | Custom Gear |
Bulk orders and OEM customization are available directly from LDB, with volume discounts and technical support included.
Why Source from LDB?
As an experienced manufacturer and supplier, LDB offers:
100% in-house production for quality control
ISO 9001 certified manufacturing
Full traceability for precision-grade bearings
Support for special materials and coatings
3–5 year warranty on precision bearings
LDB’s cross roller slewing bearings are already trusted by customers in Germany, Japan, South Korea, and the U.S. for high-tech manufacturing platforms.
Conclusion
When your application requires ultra-smooth rotation, tight dimensional tolerances, and strong rigidity in a compact form, Cross Roller Slewing Bearings are the optimal choice. From design consultation to post-delivery support, LDB offers reliable precision solutions backed by engineering expertise and global delivery capabilities.
Contact LDB today for technical support, drawings, and a quote on your next cross roller slewing bearing project.