Slewing Bearings in Wind Turbines: Ensuring Stability and Efficiency
Introduction: The Role of Slewing Bearings in Wind Energy Systems
Wind turbines are complex electromechanical systems designed to convert kinetic energy from wind into electrical power. At the heart of this process lies a set of crucial components responsible for enabling smooth rotation, efficient tracking, and structural alignment—one of the most important being the slewing bearing. Slewing bearings in wind turbines support yaw and pitch mechanisms, allowing the nacelle and blades to adjust according to wind direction and speed.
In this article, we explore how slewing bearings contribute to the performance, reliability, and longevity of wind turbines. We cover their structural features, material considerations, price implications, supplier recommendations, and highlight why LDB Bearing is a trusted manufacturer in the wind energy sector.
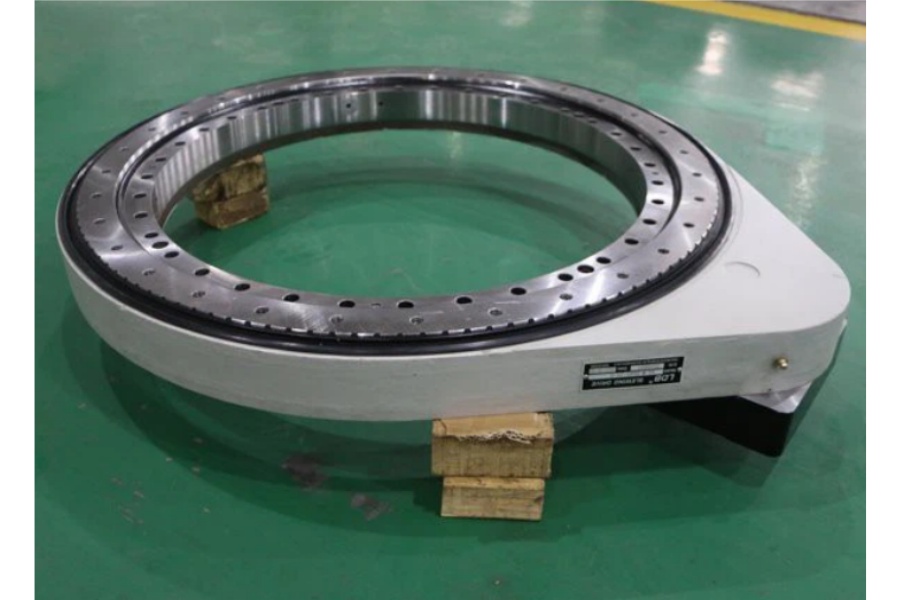
Key Functions of Slewing Bearings in Wind Turbines
Yaw System (Nacelle Rotation)
Slewing bearings enable the entire nacelle to rotate and align with wind direction. This mechanism ensures maximum energy capture and minimizes turbine stress during directional changes.
Pitch System (Blade Adjustment)
Pitch bearings adjust the angle of turbine blades in response to wind speed. This helps maintain optimal aerodynamic performance while protecting blades and the drivetrain from excessive loads.
Structural and Material Considerations
Common Slewing Bearing Types for Wind Turbines:
Four Point Contact Ball Slewing Bearing: Ideal for pitch systems due to compactness and multi-directional load capacity
Cross Roller Slewing Bearing: Suitable for yaw systems requiring higher rigidity and precision
Three-Row Roller Slewing Bearing: Used in large turbines for maximum load distribution
Preferred Materials:
42CrMo (Chromium-Molybdenum Steel): High fatigue resistance, excellent load-bearing properties
Surface Hardened Races: Induction or carburized hardened paths improve wear resistance
Corrosion-Resistant Coatings: For offshore or high-humidity environments
Load and Environmental Challenges
Slewing bearings in wind turbines must withstand:
Dynamic and Static Loads: From rotor torque and wind pressure
Temperature Fluctuations: From sub-zero climates to desert heat
Salt Spray and Moisture: In offshore installations
Low Maintenance Access: Bearings must offer long service intervals
Proper sealing, lubrication, and material selection are critical for ensuring long-term performance under these challenging conditions.
Price, Supplier, and Manufacturer Considerations
Price Factors:
Size and weight of the bearing
Load capacity and safety factors
Coating and sealing options
Custom machining requirements
While high-performance bearings for wind turbines are a significant investment, they deliver long-term value by minimizing downtime and maximizing turbine output.
Supplier and Manufacturer Requirements:
Proven track record in renewable energy sector
Compliance with IEC and ISO wind turbine bearing standards
Full traceability and testing documentation (e.g., UT, MPI, hardness)
Engineering support for integration and troubleshooting
LDB Bearing’s Solutions for Wind Turbine Applications
LDB Bearing designs and manufactures wind-turbine-specific slewing bearings with optimized structures, coatings, and service life characteristics.
Product Highlights:
Cross Roller Slewing Bearings for yaw systems: High rigidity and minimal deflection
Four Point Contact Bearings for pitch mechanisms: Compact and efficient
Customized Three-Row Roller Bearings: For large-scale turbines
Features:
Induction-hardened raceways and precision-machined rollers
Multi-layer sealing structures with salt-spray protection
Factory-lubricated and pretested units
LDB Advantage:
Direct manufacturer pricing
Global supplier network
Technical support for wind farm deployment and maintenance planning
Case Study: LDB Bearings in Offshore Wind Projects
In a 100 MW offshore wind project in Northern Europe, LDB supplied three-row roller slewing bearings with IP66-rated seals and anti-corrosion coating. After 24 months of continuous operation under high humidity and salt exposure, inspections showed no seal failures or abnormal wear, confirming LDB’s bearings as a dependable long-term investment.
Conclusion
Slewing bearings are indispensable in the efficient and safe operation of modern wind turbines. Their performance directly impacts energy output, maintenance frequency, and operational safety.
LDB Bearing stands as a reliable partner for wind turbine OEMs and operators, offering engineering-grade slewing bearing solutions tailored for both onshore and offshore applications. Whether you need precision, durability, or long service intervals, LDB delivers trusted performance at a competitive price.
To learn more or request a quote, visit www.ldb-bearing.com.
Slewing Bearings in Wind Turbines: Ensuring Stability and Efficiency
Introduction: The Role of Slewing Bearings in Wind Energy Systems
Wind turbines are complex electromechanical systems designed to convert kinetic energy from wind into electrical power. At the heart of this process lies a set of crucial components responsible for enabling smooth rotation, efficient tracking, and structural alignment—one of the most important being the slewing bearing. Slewing bearings in wind turbines support yaw and pitch mechanisms, allowing the nacelle and blades to adjust according to wind direction and speed.
In this article, we explore how slewing bearings contribute to the performance, reliability, and longevity of wind turbines. We cover their structural features, material considerations, price implications, supplier recommendations, and highlight why LDB Bearing is a trusted manufacturer in the wind energy sector.
Key Functions of Slewing Bearings in Wind Turbines
Yaw System (Nacelle Rotation)
Slewing bearings enable the entire nacelle to rotate and align with wind direction. This mechanism ensures maximum energy capture and minimizes turbine stress during directional changes.
Pitch System (Blade Adjustment)
Pitch bearings adjust the angle of turbine blades in response to wind speed. This helps maintain optimal aerodynamic performance while protecting blades and the drivetrain from excessive loads.
Structural and Material Considerations
Common Slewing Bearing Types for Wind Turbines:
Four Point Contact Ball Slewing Bearing: Ideal for pitch systems due to compactness and multi-directional load capacity
Cross Roller Slewing Bearing: Suitable for yaw systems requiring higher rigidity and precision
Three-Row Roller Slewing Bearing: Used in large turbines for maximum load distribution
Preferred Materials:
42CrMo (Chromium-Molybdenum Steel): High fatigue resistance, excellent load-bearing properties
Surface Hardened Races: Induction or carburized hardened paths improve wear resistance
Corrosion-Resistant Coatings: For offshore or high-humidity environments
Load and Environmental Challenges
Slewing bearings in wind turbines must withstand:
Dynamic and Static Loads: From rotor torque and wind pressure
Temperature Fluctuations: From sub-zero climates to desert heat
Salt Spray and Moisture: In offshore installations
Low Maintenance Access: Bearings must offer long service intervals
Proper sealing, lubrication, and material selection are critical for ensuring long-term performance under these challenging conditions.
Price, Supplier, and Manufacturer Considerations
Price Factors:
Size and weight of the bearing
Load capacity and safety factors
Coating and sealing options
Custom machining requirements
While high-performance bearings for wind turbines are a significant investment, they deliver long-term value by minimizing downtime and maximizing turbine output.
Supplier and Manufacturer Requirements:
Proven track record in renewable energy sector
Compliance with IEC and ISO wind turbine bearing standards
Full traceability and testing documentation (e.g., UT, MPI, hardness)
Engineering support for integration and troubleshooting
LDB Bearing’s Solutions for Wind Turbine Applications
LDB Bearing designs and manufactures wind-turbine-specific slewing bearings with optimized structures, coatings, and service life characteristics.
Product Highlights:
Cross Roller Slewing Bearings for yaw systems: High rigidity and minimal deflection
Four Point Contact Bearings for pitch mechanisms: Compact and efficient
Customized Three-Row Roller Bearings: For large-scale turbines
Features:
Induction-hardened raceways and precision-machined rollers
Multi-layer sealing structures with salt-spray protection
Factory-lubricated and pretested units
LDB Advantage:
Direct manufacturer pricing
Global supplier network
Technical support for wind farm deployment and maintenance planning
Case Study: LDB Bearings in Offshore Wind Projects
In a 100 MW offshore wind project in Northern Europe, LDB supplied three-row roller slewing bearings with IP66-rated seals and anti-corrosion coating. After 24 months of continuous operation under high humidity and salt exposure, inspections showed no seal failures or abnormal wear, confirming LDB’s bearings as a dependable long-term investment.
Conclusion
Slewing bearings are indispensable in the efficient and safe operation of modern wind turbines. Their performance directly impacts energy output, maintenance frequency, and operational safety.
LDB Bearing stands as a reliable partner for wind turbine OEMs and operators, offering engineering-grade slewing bearing solutions tailored for both onshore and offshore applications. Whether you need precision, durability, or long service intervals, LDB delivers trusted performance at a competitive price.
To learn more or request a quote, visit www.ldb-bearing.com.