Slew Drive Customization: Tailored Solutions for Complex Rotational Challenges
What is a Customized Slew Drive?
A customized slew drive is a precision-engineered rotation system that is specifically designed to meet unique project requirements. Unlike standard drives that are mass-produced to fit general use cases, customized slew drives are tailored to match specific load capacities, environmental conditions, space limitations, and operational goals.
This process may include modifying the gear ratio, altering the housing materials, integrating different motor interfaces (electric, hydraulic, or dual-motor setups), or adjusting mounting options. Custom slew drives are widely used in applications such as solar tracking systems, aerospace technologies, offshore platforms, and military-grade equipment, where standard configurations often fall short.
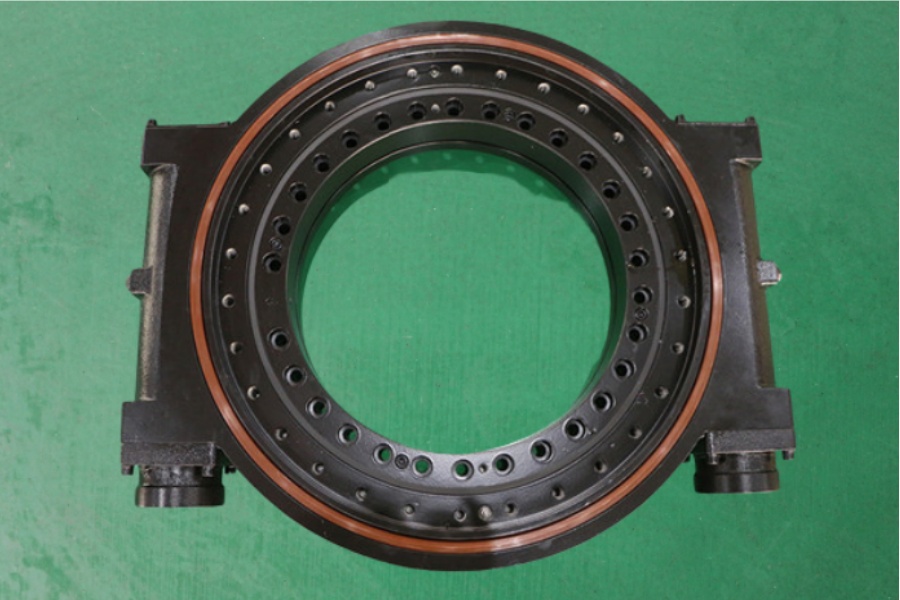
Why Do Clients Require Customization?
Unusual Load Conditions
Some applications, such as wind turbines or construction cranes, may exert dynamic loads that fluctuate rapidly and unpredictably. These situations demand specially reinforced slew drives with optimized torque resistance.
Compact or Irregular Installation Spaces
In some robotics or vehicle-mounted systems, spatial constraints require altered dimensions or novel mounting configurations.
Extreme Environmental Exposure
Custom slewing drives may need to operate in desert heat, polar cold, underwater, or corrosive atmospheres. This calls for bespoke material selection and sealing design.
Precision Control Demands
Automated machinery or positioning systems often need customized gear ratios and ultra-low backlash performance.
Common Customization Parameters
Custom Feature | Typical Options |
Gear Type | Worm, Spur, Helical, Dual Worm |
Motor Integration | Electric (DC/AC), Hydraulic, Dual-motor |
Torque Rating | From 1 kNm to over 100 kNm |
Mounting Orientation | Vertical, Horizontal, Inverted |
IP Rating (Ingress Protection) | IP65, IP66, IP67, IP68 |
Housing Material | Cast Iron, Stainless Steel, Aluminum Alloy |
Operating Temperature Range | -40°C to +80°C or higher |
LDB’s Custom Slew Drive Capabilities
As a leading manufacturer and supplier of slew drive systems, LDB specializes in offering tailored rotational solutions for clients with specialized needs. Whether you’re designing equipment for a solar farm in the Sahara or a robotic arm in a surgical facility, LDB’s engineering team can help develop a custom slew drive that fits both mechanical and operational constraints.
Key strengths include:
ISO 9001-certified production
In-house R&D and 3D prototyping
Flexible minimum order quantities
Fast response time for prototyping and revisions
Typical Applications of Customized Slew Drives
Solar Tracking Systems: With dual-axis tracking, varying installation angles, and exposure to dust or rainfall, standard drives are rarely sufficient.
Military and Defense Equipment: Customized for stealth systems, radar alignment, and rapid-response targeting.
Offshore & Marine: Designed with salt-water corrosion resistance, shock absorption, and heavy load operation in mind.
Robotics: Requiring compact, high-precision control with near-zero backlash.
Heavy Equipment: Earthmovers, cranes, and drilling rigs benefit from ultra-high torque custom drives.
Price Considerations and What Affects It
The price of a customized slew drive depends on:
The scale of customization (gearbox reengineering vs. minor mounting changes)
Torque output and precision level
Material requirements (marine-grade steel, composites, coatings)
IP rating and operating condition standards
Order volume (single unit vs. batch manufacturing)
On average:
Basic customization projects: $600 – $1500 per unit
Medium complexity: $1500 – $3500
High-torque or highly customized units: $4000+
LDB offers transparent pricing based on configuration complexity, with volume discounts available for integrators or long-term projects.
Manufacturer and Supplier Insights
LDB has over 20 years of experience as a trusted manufacturer and global supplier of high-precision slewing solutions. Working with industries across energy, automation, logistics, and defense, LDB provides:
International shipping and logistics coordination
Technical documentation and installation support
Spare parts and after-sales training
Long-term warranty and performance assurance
Why Choose LDB for Custom Slew Drives?
Technical Excellence: LDB uses advanced CNC equipment, robotic welding, and fatigue testing to ensure that every custom drive meets your project standards.
Design Flexibility: Support for both metric and imperial standards, various flange types, and custom housing shapes.
Responsive Engineering: Short lead times and collaborative engineering teams help customers develop, prototype, and validate new solutions.
Global Support Network: Sales and service partners in over 30 countries ensure smooth communication and deployment.
Conclusion
When your project demands a non-standard solution, a customized slew drive may be the only viable path forward. LDB’s tailored slewing systems ensure optimal performance, reliability, and long-term ROI. With vast experience and a commitment to engineering innovation, LDB is your ideal partner for bringing complex rotation systems to life.