How to Maintain and Extend the Life of Slewing Bearings in Harsh Environments
What Are Slewing Bearings and Why Is Maintenance Critical?
Slewing bearings are large, precision-engineered components used to support axial, radial, and overturning moment loads in rotating structures. They are commonly found in cranes, excavators, wind turbines, solar trackers, and offshore platforms. In harsh environments—such as extreme temperatures, marine conditions, dusty mines, and desert regions—proper maintenance is not optional; it’s essential.
Without routine maintenance, slewing bearings can suffer from corrosion, grease degradation, raceway wear, and premature failure. In mission-critical systems, such failures may result in expensive downtime, safety hazards, or even structural damage.
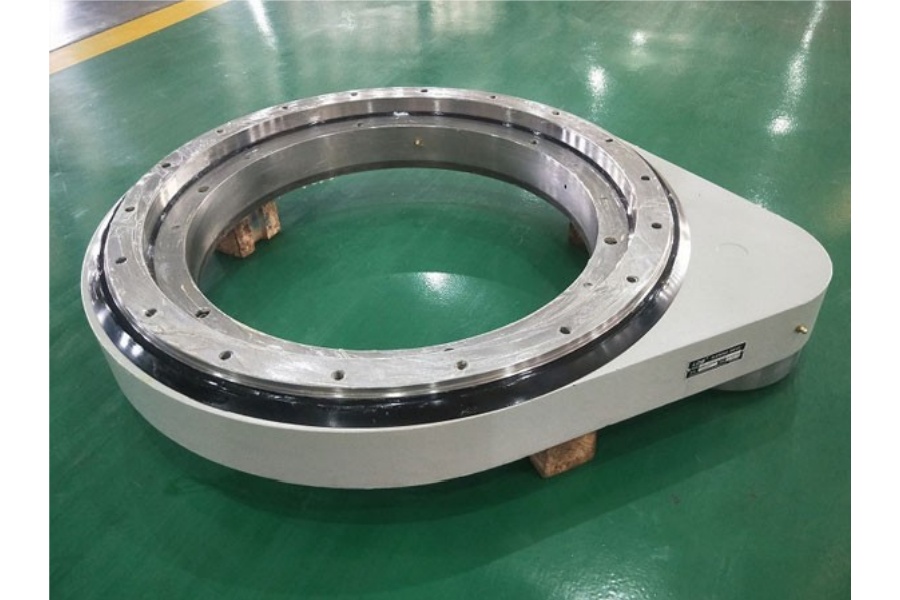
Common Environmental Challenges for Slewing Bearings
Environment | Threats |
Marine | Saltwater corrosion, humidity, biofouling |
Desert | Fine dust intrusion, temperature swings |
Arctic | Low temperatures, ice buildup |
Mining & Cement | Abrasive dust, heavy shock loads |
Offshore Wind | High humidity, salt-laden air, turbine stress |
Best Practices for Slewing Bearing Maintenance
Regular Lubrication
Use the correct grease: EP2, lithium complex, or marine-grade grease for offshore.
Lubricate every 100–200 hours of operation, or every month for idle equipment.
Apply grease at each lube point until old grease is pushed out—this flushes contaminants.
LDB Tip: Use a grease gun with pressure gauge to ensure proper penetration. LDB supplies matched grease kits for all slewing models.
Sealing System Inspection
Check for cracked, brittle, or missing seals.
In marine or desert environments, labyrinth or multi-lip seals are recommended.
Replace damaged seals immediately to prevent dust, water, or salt ingress.
LDB offers seal upgrade kits for all standard slewing rings.
Bolt Tightening and Preload Checking
Perform bolt torque checks every 500 operating hours.
Use a calibrated torque wrench; overtightening can deform the bearing ring.
Replace any corroded or elongated bolts with high-grade (10.9 or 12.9) replacements.
LDB Maintenance Kit includes torque specs for each model.
Raceway and Gear Tooth Monitoring
Use an endoscope or grease inspection to detect wear debris in raceways.
Check backlash and gear engagement every 6–12 months.
Re-lap or replace severely worn gears.
LDB bearings are manufactured with hardened raceways (HRC 55–62) and self-cleaning gear profiles for extended service life.
Corrosion Prevention
Apply anti-corrosion coatings (zinc or epoxy) to exposed areas.
Store bearings in dry, climate-controlled conditions if unused.
Use protective covers during shipment and long-term storage.
LDB offers optional anti-rust oil film, phosphate coatings, and sealed export crates.
Maintenance Tools and Spare Parts from LDB
Sealing Rings (NBR, FKM, or marine-grade)
Bolt Replacement Kits
Grease Injection Valves
Rotation Test Tools
Wear Measurement Calipers
Replacement Gear Segments
All spare parts can be ordered directly from LDB, your trusted manufacturer and supplier.
Signs Your Slewing Bearing Needs Service or Replacement
Symptom | Possible Cause |
Audible grinding | Lack of lubrication |
Uneven rotation or binding | Gear misalignment or damage |
Excessive backlash | Worn teeth or lost preload |
Grease leakage | Damaged seal |
Rust or pitting | Corrosion from water ingress |
If detected early, many issues can be resolved with on-site repair, saving costs and extending service life.
Recommended Maintenance Schedule
Task | Frequency |
Visual Inspection | Weekly |
Lubrication | Monthly or 100–200h |
Bolt Torque Check | Quarterly |
Gear/Backlash Measurement | Semi-annually |
Seal Inspection | Annually |
LDB provides a downloadable Maintenance Log Sheet and PDF checklist tailored to your specific bearing model.
Why LDB Bearings Last Longer
Hardened raceways with deep quenching
360° sealing options for extreme conditions
High-precision machining (≤0.01mm runout)
Tested under vibration and salt spray simulations
Customized gear treatments for heavy-duty wear resistance
As a seasoned manufacturer and global supplier, LDB delivers reliability, from steel selection to surface treatment.
Conclusion
Slewing bearings are not “fit and forget” components—especially in harsh environments. By adopting a proactive maintenance routine and sourcing spare parts from trusted suppliers like LDB, you extend bearing life, improve system safety, and reduce lifecycle costs.
�� Reach out to LDB for maintenance kits, custom protection options, or service training tailored to your application.