Integrating Slew Drives with Control Systems for Enhanced Automation
Introduction: Why Slew Drive Integration Matters in Automation
In today’s era of intelligent manufacturing and autonomous systems, motion control precision and system responsiveness are no longer optional—they are fundamental. Slew drives, which combine a slewing bearing and gear mechanism in one compact unit, are essential for applications requiring controlled rotation and load-bearing performance. When integrated effectively with control systems such as PLCs (Programmable Logic Controllers), sensors, and actuators, slew drives become powerful enablers of automation, productivity, and reliability.
This article explores how slew drives can be seamlessly integrated with various control architectures, what technical factors must be considered, the cost implications, and why LDB Bearing is a trusted manufacturer and supplier in the automation space.
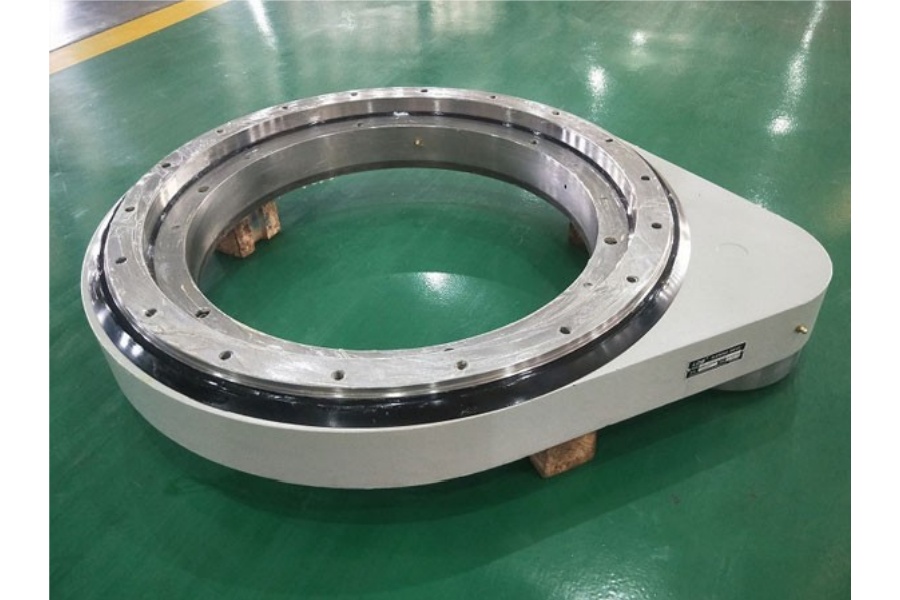
The Basics of Slew Drive Control Integration
Slew drives typically interface with one of the following motion control systems:
Programmable Logic Controllers (PLC)
Microcontroller Units (MCU)
Industrial PCs (IPC)
Closed-loop feedback systems (with encoders)
Integration involves connecting the slew drive’s input (usually a motor or actuator) to the control system that regulates speed, direction, torque, and position.
Core Components in an Integrated Setup:
Slew drive (worm or spur gear based)
Motor (DC, AC, stepper, or servo)
Encoder or position sensor
Controller (PLC/MCU/IPC)
Power supply and relays
Communication interface (CAN, RS485, Modbus, etc.)
Key Integration Considerations
Motor Compatibility
Slew drives from LDB can be adapted for various motor types:
DC Motors: Simple control, ideal for small automation tasks
AC Motors: Industrial grade, cost-efficient for heavy machinery
Servo Motors: High-precision motion control with feedback
Position Feedback and Encoders
Rotary encoders enable closed-loop control, enhancing positioning accuracy
Important for solar tracking, robotic joints, and CNC automation
Load and Torque Calculations
Control algorithms should account for backlash, moment loads, and wind-up torque
Slew drives with high gear ratios (e.g., VE or SDE series) improve resolution
IP Rating and Environmental Protection
Ensure communication and power connectors match the IP rating of the slew drive (IP65–IP66)
Sealed enclosures are recommended for outdoor or dusty environments
Industrial Applications Benefiting from Control Integration
Robotic Arms and End-Effectors: Smooth, repeatable rotation in joint actuators
Solar Tracking Systems: Automated alignment with sun angle for improved efficiency
Material Handling and Conveyor Systems: Automated rotation for load transfer
CCTV and Surveillance Systems: Precision positioning for PTZ cameras
Cranes and Lifts: Motion control of rotation axis under load
Price, Supplier, and Manufacturer Impact
Price Factors
System integration adds to initial cost (motor, encoder, controller, wiring)
However, ROI improves through better uptime, energy efficiency, and reduced human intervention
Supplier Checklist
Pre-assembled motor-gear packages
Encoder and control interface support
Wiring diagrams and API support for easy PLC integration
Manufacturer Checklist
Custom flange or motor adapter design
Material choices that support heat and electromagnetic shielding
Engineering documentation and lifecycle testing data
LDB Bearing: Engineered for Integrated Automation
LDB Bearing offers a range of slew drives that are optimized for system-level integration. Whether you are designing a custom automation platform or retrofitting legacy equipment, LDB provides full mechanical and electrical support.
Featured Products:
SE Series Slew Drive: Compact footprint, great for low-voltage control integration
VE Series Slew Drive: High-precision platform with encoder-ready configuration
SDE-PDE Series: Dual-axis automation systems, perfect for solar tracking
Customized Drive Systems: Fully integrated with servo motor and control wiring
LDB Advantages:
ISO-certified manufacturing and precision gear machining
Global supplier network and inventory support
Direct-from-manufacturer pricing and quick lead times
Electrical and mechanical integration kits available
Case Study: LDB Drives in Automated Logistics
In a Southeast Asian automated storage and retrieval system (AS/RS), LDB’s SE Series slew drives were integrated with PLC-controlled robotic shuttles. Through closed-loop servo feedback, the system achieved sub-1° rotation accuracy, improving loading/unloading speeds by 22% compared to previous pneumatic rotators.
Conclusion
Slew drives become exponentially more powerful when integrated into control systems. Precision positioning, reduced maintenance, and remote operability are just some of the benefits. For OEMs and integrators, partnering with a manufacturer that understands both mechanical and electronic requirements is key.
LDB Bearing provides not just slew drives, but total integration solutions—making them a top choice for advanced automation needs.
Explore technical documentation or get a quote at www.ldb-bearing.com.