Comparing Spur and Helical Gears: Which Is Right for Your Application?
Introduction: The Importance of Choosing the Right Gear Type
In mechanical engineering and industrial automation, gear selection is foundational to ensuring performance, efficiency, and reliability. Among the most common types of gears used in gear drives and motion systems are spur gears and helical gears. While both serve the purpose of transmitting torque and motion, they differ significantly in design, performance, application suitability, and cost.
This article compares spur and helical gears in detail, including their structural differences, functional advantages and drawbacks, cost considerations, supplier recommendations, and use cases. We also examine why LDB Bearing offers precision-manufactured spur gear drives tailored to diverse industrial needs.
Structural Overview: Spur vs. Helical Gears
Spur Gears
Teeth are straight and parallel to the gear axis
Engage simultaneously across the entire face width
Typically used in low to moderate speed applications
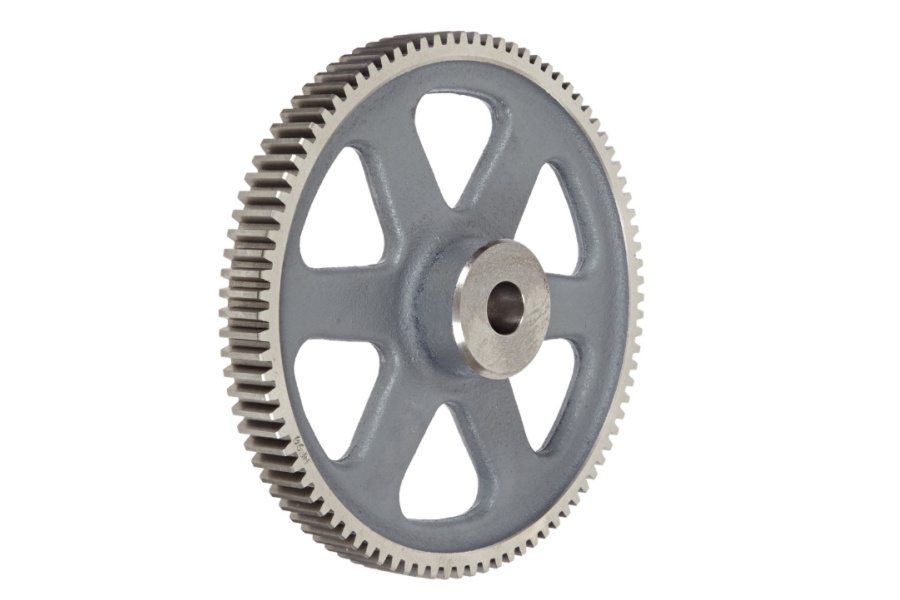
Helical Gears
Teeth are cut at an angle to the axis (helix angle)
Engage gradually, creating smoother torque transfer
Can handle higher speeds and loads
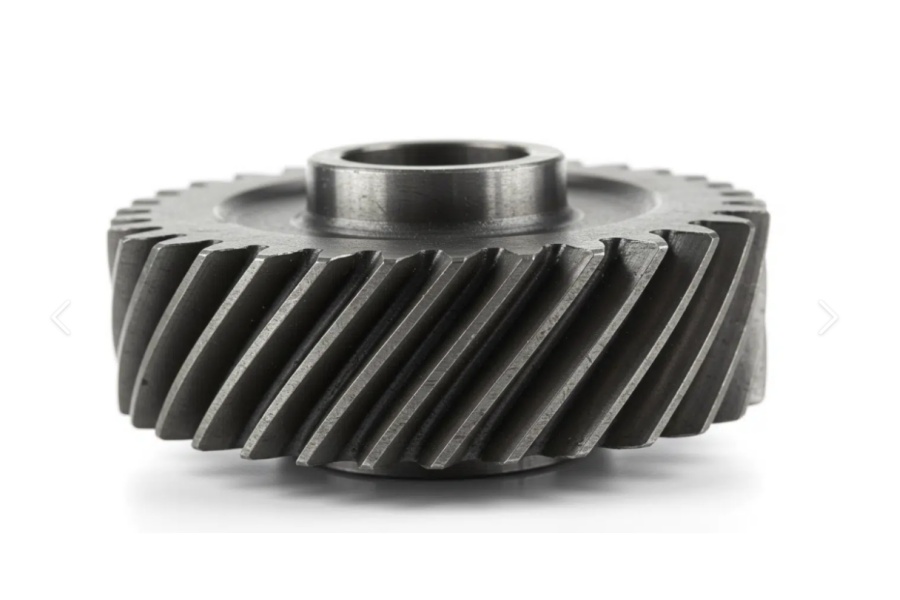
Performance Comparison
Noise and Vibration
Spur Gears: Noisier due to abrupt tooth engagement
Helical Gears: Quieter and smoother due to gradual meshing
Load Capacity
Spur Gears: Suitable for moderate loads
Helical Gears: Higher load-carrying capacity due to broader contact area
Efficiency
Spur Gears: Higher mechanical efficiency (~98–99%)
Helical Gears: Slightly lower due to axial thrust and sliding friction (~96–98%)
Axial Load
Spur Gears: No axial thrust; simplifies bearing design
Helical Gears: Generates axial thrust; requires thrust bearings
Application Suitability
Best Use Cases for Spur Gears:
Automation machinery (e.g., pick-and-place systems)
3D printers and small robotics
Precision positioning equipment
Packaging machines
Best Use Cases for Helical Gears:
Automotive transmissions
High-speed conveyors
Heavy-duty industrial gearboxes
Air compressors and turbines
Price Considerations
From a procurement perspective, spur gears are typically more cost-effective to produce due to:
Simpler manufacturing process
No need for additional axial load compensation
Lower installation and maintenance costs
Helical gears tend to be more expensive because:
More complex machining
Additional thrust bearings required
Higher-grade lubrication and thermal management
When evaluating gear pricing, it’s essential to factor in not only the unit cost but also the long-term cost of operation and maintenance. For many low- to mid-load automation tasks, spur gears offer the best value.
Supplier and Manufacturer Insights
When sourcing gear drives, consider the following:
Supplier certification: ISO, CE, and quality control standards
Manufacturer support: Custom sizing, material options, and testing documentation
Lead time and inventory: Timely availability for maintenance and expansion
Cost transparency: A good supplier will offer tiered pricing and technical support
LDB Bearing is a trusted manufacturer of spur gear drives with a proven track record in providing both standard and custom gear configurations.
LDB Bearing’s Spur Gear Drive Solutions
LDB offers a range of spur gear drives optimized for precision, efficiency, and affordability:
Product Highlights:
SG-I Spur Gear Drive: Compact, lightweight, and perfect for small automation systems
SG-M Spur Gear Drive: Mid-size unit for robotic and control applications
SG-H Spur Gear Drive: Heavy-duty, high-precision system for industrial machinery
Spur Gear Drive Customized: Fully tailored to meet unique torque, size, and mounting needs
Key Advantages:
Precision-machined gears with minimal backlash
Hardened steel for durability
Direct-from-manufacturer pricing
Available globally through certified suppliers
Decision Guide: Spur or Helical Gear?
Parameter | Spur Gear | Helical Gear |
Noise Level | Moderate to High | Low |
Load Handling | Medium | High |
Cost | Lower | Higher |
Maintenance | Simpler | More Complex |
Efficiency | Higher (98–99%) | Slightly Lower (96–98%) |
Preferred Use | Automation, Robotics | Automotive, Heavy Machinery |
Choose spur gears if:
You need affordability and simplicity
Your system runs at moderate speeds
Precision and low backlash are priorities
Choose helical gears if:
You require higher load capacity and noise reduction
Your system runs at high speeds
You have the infrastructure to support thrust bearings
Conclusion
Both spur and helical gears have their place in industrial and automation design. Understanding their mechanical properties, cost structures, and compatibility with your specific use case is key to long-term operational success.
LDB Bearing provides dependable spur gear drives backed by expert support, precision manufacturing, and scalable production. Whether you’re equipping a new automation line or replacing an existing system, LDB’s gear drives deliver reliable performance at a competitive price.
For technical consultations or quotations, visit www.ldb-bearing.com.