При покупке поворотных подшипников производители поворотных подшипников рекомендуют нам регулярно смазывать подшипники, но для тех, кто не понимает, во время смазки может возникнуть неправильная смазка. В таком случае, серьезны ли последствия неправильной смазки опорно-поворотных устройств? ? Что произойдет, если поворотный подшипник неправильно смазан? На что следует обратить внимание при смазке подшипников?
Последствия неправильной смазки опорно-поворотных устройств
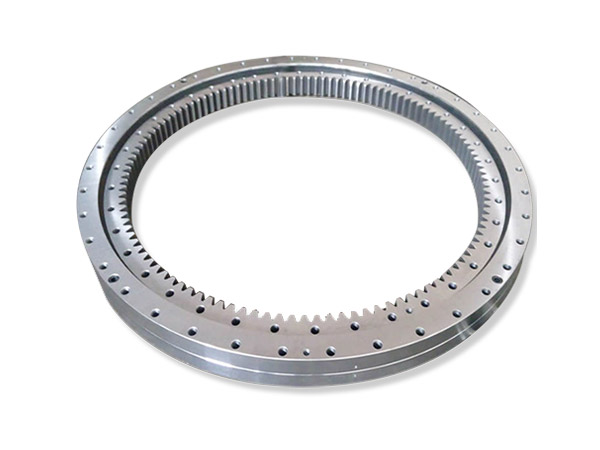
1. Обесцвечивание
Контакт металл-металл приведет к слишком высокой температуре подшипника, что приведет к обесцвечиванию дорожек качения и роликов. В легких случаях это изменение цвета происходит из-за загрязнения смазкой поверхности подшипника, а в тяжелых случаях – из-за обесцвечивания металла из-за высоких температур. Во всех случаях раннее обнаружение позволяет избежать дорогостоящего ремонта.
2. Подогрев подшипников.
Во время работы машины часть, на которой установлен подшипник, может иметь определенную температуру. При прикосновении к корпусу механизма рукой должно быть нормально, что вы не чувствуете тепла, в противном случае это указывает на слишком высокую температуру подшипника. Одна из причин слишком высоких подшипников – плохая смазка подшипников. Смазочное масло (или консистентная смазка), используемое в подшипниках качения, имеет определенную рабочую температуру. Когда температура слишком высока, вода или зола попадают в гнездо подшипника, оно серьезно окисляется, превращается в эмульсию и т. Д., Что теряет свой смазывающий эффект и приводит к тому, что подшипник страдает от высокой температуры. И сгорел. Кроме того, низкое качество самого смазочного масла (или консистентной смазки) или отсутствие добавления масла (консистентной смазки) во время работы приведет к повышению температуры подшипника.
3. Царапины и шелушение.
Осмотрите подшипник на предмет порезов или отслаивания металла. Эти ситуации требуют немедленного внимания. Царапины и отслаивание могут возникать при высоких нагрузках и низких оборотах или при постоянных высоких температурах, а тонкая или недостаточная масляная пленка ускоряет возникновение проблемы. Недостаточная смазка, неправильный выбор смазки или резкие изменения условий работы могут привести к отслаиванию материала подшипника или появлению царапин на ребрах подшипника.
4. Ненормальный шум подшипников.
Если подшипник находится в хорошем состоянии непрерывного вращения, он будет издавать тихий воющий или жужжащий звук. Если слышно резкое шипение, скрип и другие нерегулярные звуки, это часто указывает на то, что подшипник находится в плохом состоянии непрерывного вращения. Резкий скрип может быть вызван неправильной смазкой.
5. Подшипник полностью заблокирован.
Сильный местный нагрев приведет к течению металла в подшипнике, что приведет к изменению исходного материала и геометрии подшипника. Это может привести к чрезмерному наклону роликов, повреждению сепаратора и полной блокировке подшипника. В случае катастрофического повреждения рекомендуется проконсультироваться со специалистом по подшипникам, чтобы определить основную причину проблемы, поскольку это может быть не только смазка, но и другой фактор.
Меры предосторожности для правильной смазки
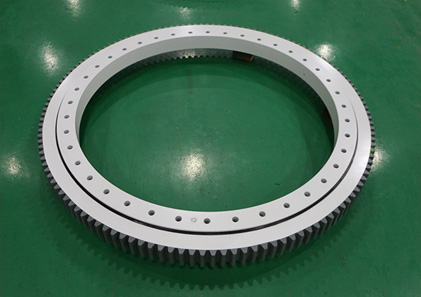
1. Выберите подходящую смазку.
Выбор подходящей консистентной смазки позволит ей полностью выполнять роль смазки в работе подшипника, так что подшипник может использоваться в течение более длительного времени. Ниже приведены моменты, на которые необходимо обратить внимание при выборе смазки. Давайте взглянем.
(1) Посмотрите на рабочую температуру: рабочая температура смазочной части является важной основой для выбора консистентной смазки. Типичными компонентами, в которых используется консистентная смазка, являются подшипники качения. В условиях высоких температур температура наружного кольца подшипника на 15 ° C ниже, чем температура внутреннего кольца. Температура подшипника, работающего на средних и низких оборотах (3000-5000р / мин), аналогична температуре внутренней среды. В условиях низких температур необходимо использовать синтетическую масляную консистентную смазку, особенно для некоторых миниатюрных подшипников инструментов, которые имеют небольшой аэродинамический крутящий момент. Особое внимание уделите подбору смазки.
(2) Посмотрите на скорость вращения подшипника: скорость смазочного компонента имеет большое влияние на срок службы подшипника консистентной смазки. Поэтому при выборе консистентной смазки необходимо учитывать скорость движения смазываемой детали.
(3) Обратите внимание на окружающую среду: среда, в которой находится смазочная часть и контактирующая среда, имеют большое влияние на характеристики пластичной смазки.
(4) Посмотрите на метод заполнения: метод заполнения консистентной смазкой включает ручное заполнение и централизованное заполнение насоса. Смазка или заполнение, заполнение шприца для смазки, заполнение стакана для жира и т. Д. – это ручное заполнение и автоматическое заполнение.
2. Выберите правильный путь
(1) Ручная смазка: это относительно примитивный метод. В случае недостаточного количества смазочного масла в подшипнике используйте масленку для подачи масла. Обычно он используется при малой нагрузке, низкой скорости или прерывистом движении. Во время работы рекомендуется использовать маслозаливное отверстие. На него устанавливают пылезащитный колпак или шаровой кран, а в качестве фильтрующих устройств используют войлок, вату, шерсть и т. Д.
(2) Автоматическая смазка: автоматический лубрикатор – это устройство, используемое для замены ручной дозаправки. Главное преимущество этого устройства – экономия труда. Он может заправляться регулярно и количественно, так что срок службы оборудования может быть продлен, особенно подходит для более сложных условий работы. Внизу, может снизить риск ручной дозаправки. Используя автоматический лубрикатор, вы можете непрерывно автоматически смазывать работающее оборудование.
3. Своевременно добавляйте смазку.
Выбор подходящей консистентной смазки и метода смазки является предпосылкой для смазки, но также необходимо своевременно добавлять смазку при ежедневном использовании. Это тоже проблема, которую люди часто игнорируют или забывают. Своевременная добавка смазки гарантирует, что подшипник работает в соответствии с условиями эксплуатации. Смазочное масло, которое также является ключом к продлению срока службы подшипника.
Сказанное выше является полным содержанием последствий, вызванных неправильной смазкой поворотного подшипника и методом смазки. Мы понимаем, что неправильная смазка поворотного подшипника может привести к изменению цвета подшипника, нагреву, появлению царапин и отслаиванию, возникновению ненормального шума, блокировке и т. Д. При смазке обращайте внимание на правильный выбор смазки, своевременно добавляйте смазку и т. Д. , что может эффективно предотвратить возникновение неправильной смазки.